In today’s fast-paced eCommerce and retail landscape, order fulfillment cycle time plays a pivotal role in shaping customer experiences and operational efficiency. Imagine placing an online order and receiving it faster than expected—chances are, you’d return to that store, right? That’s the magic of an optimized fulfillment process.
At its core, order fulfillment cycle time measures how quickly a business can process, prepare, and deliver an order from the moment it’s placed to the time it reaches the customer. A shorter cycle time not only enhances customer satisfaction but also boosts a company’s competitive edge by streamlining supply chain operations.
For businesses aiming to scale or retain customer trust, mastering this metric is essential. In this blog, we’ll learn the definition, calculation, and strategies to improve order fulfillment cycle time to create seamless customer experiences while driving operational success.
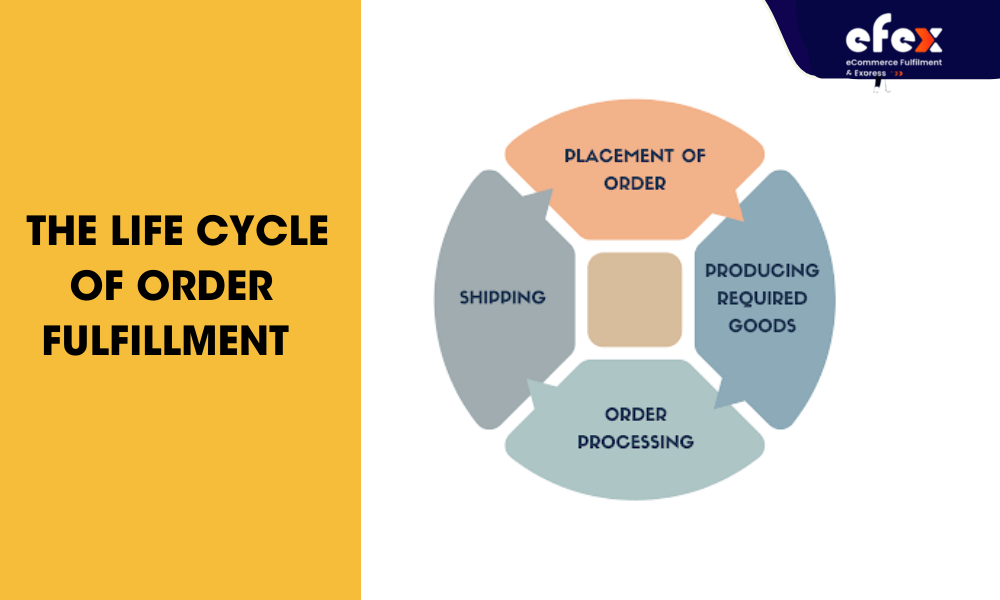
Credit: EFEX
What is Order Fulfillment Cycle Time?
Order fulfillment cycle time is the total amount of time it takes to complete the entire process of fulfilling a customer’s order, starting from the moment the order is placed until the product is delivered to the customer. It serves as a key performance metric in supply chain management, offering insights into the efficiency and responsiveness of a business's operations.
This metric is critical because it directly affects customer satisfaction, operational efficiency, and the overall success of the supply chain. The shorter and more accurate the cycle time, the better a company can meet customer expectations and maintain a competitive edge.
Why is Order Fulfillment Cycle Time Important?
- Improved Customer Experience: A faster cycle time ensures quicker deliveries, enhancing customer satisfaction and loyalty.
- Operational Efficiency: Shorter cycle times reduce bottlenecks in the supply chain, optimize resource allocation, and lower operational costs.
- Competitiveness: In today’s fast-paced market, businesses that streamline their fulfillment processes can stay ahead of competitors.
Key Components of Order Fulfillment Cycle Time
- Order Placement: When the customer places an order online or in-store.
- Order Processing: Verification, picking, and packing of the order.
- Shipping and Delivery: The time taken to dispatch and deliver the product to the customer.
- Final Receipt: The completion of the delivery process and customer acknowledgment.
Difference Between Order Fulfillment Cycle Time and Lead Time
Although order fulfillment cycle time and lead time are closely related, they represent distinct aspects of the supply chain:
1. Order Fulfillment Cycle Time
- Refers to the customer-facing part of the process.
- Tracks the time from when an order is placed by a customer to when it is delivered.
- Focused on order management, shipping, and delivery logistics.
Example: A customer orders a product online. The time it takes to process, ship, and deliver this product constitutes the order fulfillment cycle time.
2. Lead Time
- Broader in scope and includes the time it takes for goods to be manufactured or sourced before becoming available for sale.
- Encompasses supplier processes, production schedules, and delivery to the business.
- Relevant to inventory and supply chain planning.
Example: A retailer orders stock from a supplier. The time required for the supplier to produce and ship the stock to the retailer’s warehouse is the lead time.
Why is Order Fulfillment Cycle Time Important?
Order fulfillment cycle time plays a pivotal role in shaping the success of a business. It is a critical metric that directly impacts customer satisfaction, operational efficiency, and overall business growth. By understanding and optimizing this metric, companies can enhance their performance, meet customer expectations, and stay competitive in today’s fast-paced market.
Gauging Customer Satisfaction
The speed and accuracy of order fulfillment are key drivers of customer satisfaction. When customers receive their orders on time and without errors, it fosters trust and loyalty toward the brand.
- Quick Delivery Expectations: In the age of same-day and next-day delivery services, customers expect their orders to arrive promptly. A shorter fulfillment cycle time ensures these expectations are met.
- Building Brand Loyalty: Reliable and timely deliveries leave a positive impression, encouraging repeat purchases and word-of-mouth recommendations.
- Reducing Customer Complaints: Delays or errors in the fulfillment process can lead to dissatisfaction and negative reviews. Monitoring cycle time helps businesses identify and address issues proactively.
Detecting Supply Chain Inefficiencies
Order fulfillment cycle time is a valuable metric for identifying bottlenecks and inefficiencies within the supply chain. By analyzing this data, businesses can uncover areas that need improvement, such as inventory management, warehouse organization, or shipping processes.
- Pinpointing Delays: Monitoring the time taken at each stage of the fulfillment process helps detect where delays are occurring, whether in order processing, picking, packing, or shipping.
- Optimizing Operations: Businesses can use cycle time insights to streamline workflows, reduce waste, and allocate resources more effectively.
- Enhancing Supply Chain Visibility: Understanding the flow of orders through the supply chain allows companies to anticipate disruptions and adjust accordingly.
Example: A fulfillment center that discovers a delay in the picking process can implement automation or better training to improve efficiency.
Scaling Readiness for Business Growth
A well-optimized order fulfillment cycle time indicates that a business is prepared to scale operations effectively. As demand increases, the ability to fulfill orders quickly and accurately becomes even more critical.
- Handling Increased Volume: Shorter cycle times show that a company’s fulfillment infrastructure can handle growth without sacrificing quality or speed.
- Attracting New Customers: Efficient fulfillment processes lead to positive customer experiences, making the brand more attractive to potential buyers.
- Reducing Costs: Streamlined operations minimize waste and overhead, allowing businesses to reinvest in growth strategies such as marketing, product development, or global expansion.
Example: A company with a scalable fulfillment process can seamlessly expand into new markets, offering the same fast and reliable service to a broader audience.
Factors Affecting Order Fulfillment Cycle Time
Efficient order fulfillment cycle time relies on multiple interconnected factors. Optimizing these areas can significantly improve delivery speed, accuracy, and customer satisfaction.
Inventory Management
Effective inventory management is crucial for fulfilling orders on time.
- Stock Levels: Maintaining optimal stock prevents delays due to backorders or overstock issues.
- Tracking Systems: Real-time tracking ensures accurate availability data and minimizes errors.
Warehouse Organization
A well-organized warehouse reduces picking, packing, and shipping times.
- Layout Efficiency: Logical placement of high-demand items speeds up retrieval.
- Clear Labeling: Proper labeling ensures quick and accurate identification of products.
Order Processing Technology
Advanced technology enhances efficiency and minimizes errors during order fulfillment.
- Automation Tools: Tools like barcoding, RFID, and order management systems streamline workflows.
- Integrated Software: Systems like Warehouse Management Systems (WMS) enable seamless coordination across operations.
Data Accuracy
Accurate data is critical for smooth operations and timely deliveries.
- Real-Time Updates: Ensure that inventory levels, order details, and shipping statuses are updated consistently.
- Minimize Errors: Double-check input data to avoid costly mistakes that slow down the process.
Shipping Partners
Reliable shipping partners play a key role in maintaining fulfillment timelines.
- Partner Selection: Evaluate shipping providers based on delivery speed, reliability, and geographic reach. Use reliable suppliers like Spocket for faster and smooth delivery.
- Tracking Capabilities: Work with partners offering robust tracking systems to keep customers informed.
How to Calculate Order Fulfillment Cycle Time
Understanding order fulfillment cycle time is essential for measuring supply chain efficiency and identifying areas for improvement. Let’s explore the formula and real-life examples to illustrate its application across various sectors.
Order Fulfillment Cycle Time Formula
The formula for order fulfillment cycle time is
Order Fulfillment Cycle Time = (Delivery Date - Order Received Date)
This formula measures the total time from when an order is placed to when it is delivered to the customer. For a more granular analysis, businesses can break it down into stages such as processing, packaging, and shipping.
Example Calculation
- Order Received Date: January 1, 2024
- Order Delivered Date: January 5, 2024
- Cycle Time: 5 - 1 = 4 days
For businesses, tracking this metric regularly ensures smoother operations and improved customer satisfaction.
Real-Life Examples Across Different Sectors
Cycle Time in Manufacturing
In manufacturing, cycle time includes raw material procurement, production, and shipment.
Example: A car manufacturer takes 20 days to source parts, assemble vehicles, and deliver them to dealerships.
Cycle Time in Procurement
Procurement cycle time tracks the time between placing a purchase order and receiving goods.
Example: A retailer orders products from a supplier, and it takes 10 days for the inventory to arrive.
Cycle Time in Logistics
Logistics cycle time includes warehousing, freight movement, and final delivery.
Example: A logistics company delivers packages in 2 days through optimized routes and real-time tracking.
Cycle Time in eCommerce
eCommerce businesses calculate cycle time from online order placement to delivery.
Example: An eCommerce store fulfills an order within 3 days using an automated warehouse and fast shipping partners.
Benefits of Improving Order Fulfillment Cycle Time
Improving your order fulfillment cycle time isn’t just about faster deliveries; it’s a cornerstone of long-term business success. Here are the key benefits of optimizing this crucial metric.
Creates Brand Loyalty
Fast and reliable order fulfillment leads to repeat customers, who appreciate consistency and efficiency. When buyers receive their orders on time, it reinforces their trust in your brand. Studies reveal that 73% of consumers say delivery speed heavily influences their loyalty to a retailer. By exceeding expectations, your brand becomes their go-to choice.
Builds Customer Trust
Timely order fulfillment assures customers of your business's reliability. It sends a message that their satisfaction is your priority. Transparency in shipping timelines and prompt deliveries create a positive shopping experience, building a foundation of trust that encourages glowing reviews and word-of-mouth referrals.
Attracts New Customers
Satisfied customers are your best marketers. Fast fulfillment encourages them to leave positive feedback, which attracts new buyers. Additionally, speedy deliveries give you an edge over competitors. In an age where next-day or same-day shipping is highly valued, businesses with streamlined fulfillment processes capture a larger audience.
Enhances Operational Efficiency
Optimizing your order fulfillment cycle time reduces bottlenecks and enhances overall efficiency. With better processes in inventory management, warehouse organization, and shipping, you lower operational costs and avoid errors like stockouts or delayed shipments. This streamlined workflow not only saves time but also maximizes profits.
The Impact of Order Fulfillment Cycle Time on Business Performance
The order fulfillment cycle time significantly influences how a business operates and is perceived in the market. Here’s how it affects key aspects of business performance:
Customer Satisfaction and Retention
Quick and reliable order fulfillment directly enhances customer satisfaction, a critical factor in retention. A shorter cycle time ensures customers receive their orders promptly, meeting or exceeding their expectations. Happy customers are more likely to return for repeat purchases and recommend your business to others. According to a study by HubSpot, 93% of customers are likely to make repeat purchases with businesses that offer excellent service, including timely deliveries.
Competitive Advantage in the Market
In today’s fast-paced eCommerce landscape, consumers expect swift deliveries. Businesses with optimized order fulfillment cycle times can outperform competitors by offering faster, more efficient service. Whether it’s next-day delivery or accurate real-time updates, a reduced cycle time positions your business as a market leader, appealing to time-sensitive shoppers.
Cost Implications
Inefficient order fulfillment leads to increased operational costs, including storage, labor, and expedited shipping fees to compensate for delays. Streamlining the cycle time minimizes these expenses by ensuring smooth inventory turnover and reducing the need for last-minute fixes. Lower costs contribute to higher profit margins and enable competitive pricing.
Strengthening Brand Reputation
Your order fulfillment process is a reflection of your business’s reliability and professionalism. Consistently meeting delivery promises strengthens your brand's reputation in the eyes of customers. A strong reputation not only attracts new buyers but also builds long-term trust with existing ones, paving the way for sustainable growth.
Tools and Technology for Improving Order Fulfillment Cycle Time
Leveraging the right tools and technology can significantly enhance your order fulfillment cycle time, ensuring faster and more accurate delivery of products. Here are some key tools and their roles in improving fulfillment efficiency:
Inventory Management Software
Inventory management software streamlines the process of tracking and managing stock levels, preventing delays caused by stockouts or overstocking. It provides real-time visibility into inventory, helping businesses maintain optimal stock levels.
Key Benefits
- Reduces order processing delays by ensuring inventory accuracy.
- Minimizes costs associated with overstocking or urgent restocking.
- Integrates with order processing systems for seamless workflows.
Popular Tools: Zoho Inventory, TradeGecko, Cin7
Warehouse Management Systems (WMS)
A warehouse management system (WMS) optimizes warehouse operations, from receiving and storing goods to picking, packing, and shipping orders. WMS ensures efficient space utilization and faster order processing.
Key Benefits
- Enhances picking and packing accuracy, reducing errors.
- Optimizes warehouse layout for faster movement of goods.
- Tracks inventory movement for real-time updates.
Popular Tools: Fishbowl, Manhattan Associates, SAP Warehouse Management.
Analytics and Reporting Tools
Analytics and reporting tools enable businesses to monitor key performance metrics related to order fulfillment. By analyzing data, companies can identify bottlenecks and areas for improvement.
Key Benefits
- Tracks metrics like cycle time, order accuracy, and shipping delays.
- Provides actionable insights to optimize workflows.
- Helps in benchmarking performance against industry standards.
Popular Tools: Google Analytics, Tableau, Microsoft Power BI
AI-Driven Demand Forecasting
AI-driven demand forecasting uses machine learning algorithms to predict future demand based on historical data, trends, and seasonality. Accurate forecasting helps align inventory levels with anticipated demand.
Key Benefits
- Reduces overstock and stockout situations.
- Enhances supplier collaboration with accurate demand planning.
- Improves overall supply chain efficiency.
Popular Tools: NetSuite Demand Planning, GMDH Streamline, Blue Yonder
Ways to Improve Order Fulfillment Cycle Time
Improving your order fulfillment cycle time is essential to boosting efficiency, meeting customer expectations, and staying competitive in today’s fast-paced market. Here are proven strategies to optimize this critical metric.
Optimize Inventory Management
Effective inventory management ensures that products are available when needed, reducing delays in order processing and fulfillment.
- Implement Real-Time Tracking: Use inventory management software to monitor stock levels in real time, preventing stockouts or overstocking.
- Use ABC Analysis: Categorize inventory based on demand and prioritize frequently sold items for faster access.
- Automate Reordering: Set up automated reordering to maintain optimal inventory levels and avoid fulfillment disruptions.
Enhance Warehouse Organization
A well-organized warehouse significantly reduces the time spent picking, packing, and shipping orders.
- Optimize Layouts: Arrange items in a way that minimizes travel time for warehouse staff, such as storing high-demand products closer to packing stations.
- Use Zone Picking: Divide the warehouse into zones to streamline the picking process for large orders.
- Label and Organize Clearly: Use proper labeling and categorization to make locating items faster and more accurate.
Leverage Advanced Order Processing Technology
Investing in the right order processing technology can automate and speed up key stages of the fulfillment cycle.
- Adopt Warehouse Management Systems (WMS): These tools optimize picking, packing, and inventory tracking processes.
- Use Barcode Scanners and RFID: These technologies improve accuracy and reduce manual errors during order processing.
- Integrate AI and Automation: Automate repetitive tasks like label generation, invoice creation, and order sorting for faster processing.
Choose the Right Shipping Partners
Selecting reliable shipping partners ensures timely deliveries and enhances customer satisfaction.
- Assess Performance Metrics: Evaluate shipping partners based on on-time delivery rates, shipping costs, and coverage.
- Offer Multiple Shipping Options: Provide customers with various options, such as express delivery or standard shipping, to cater to their preferences.
- Monitor Shipping Timelines: Use tracking tools to keep tabs on delivery performance and identify delays proactively.
Track and Analyze Metrics Regularly
Regularly monitoring order fulfillment metrics helps identify inefficiencies and areas for improvement.
- Key Metrics to Track: Measure metrics like order cycle time, pick-and-pack time, and shipping accuracy.
- Set Benchmarks: Compare performance against industry standards to identify where improvements are needed.
- Use Data Analytics Tools: Analyze historical data to uncover trends and optimize fulfillment processes.
Consider Local vs. Global Sourcing for Materials
Sourcing decisions can significantly impact fulfillment times, especially for businesses relying on imported materials.
- Local Sourcing: Reduces lead times and shipping costs, making it ideal for high-demand items or fast-moving products.
- Global Sourcing: May be more cost-effective for bulk purchases but requires robust planning to mitigate delays.
- Hybrid Approach: Combine local and global sourcing for a balanced strategy that minimizes costs while maintaining agility.
Use Reliable Suppliers and Accurate Demand Forecasting
Collaborating with trustworthy suppliers and forecasting demand accurately helps maintain a seamless supply chain.
- Partner with Reliable Suppliers: Ensure suppliers can meet your quality standards and deliver on time consistently.
- Implement Demand Forecasting: Use tools like predictive analytics to anticipate customer needs and stock up accordingly.
- Establish Buffer Stock: Maintain safety stock levels to avoid fulfillment delays during peak periods or unexpected surges in demand.
Conclusion
Understanding and optimizing your order fulfillment cycle time is crucial for ensuring customer satisfaction and staying competitive in today’s fast-paced market. By streamlining processes, leveraging automation, and partnering with reliable suppliers, you can significantly reduce delays and improve overall efficiency. Platforms like Spocket offer a wide range of dependable suppliers, enabling faster processing and delivery of orders. A reliable supplier network not only shortens cycle times but also enhances customer trust and loyalty. Take proactive steps to refine your fulfillment process, and choose trusted partners like Spocket to deliver a seamless shopping experience for your customers.